- Blog
Manufacturing Data Analytics: Maximizing Production Efficiency
Ever wondered why some manufacturing plants seem to run like clockwork while others constantly battle inefficiencies? The secret often lies in how they handle their data. Manufacturing data analytics has become a game-changer in modern production facilities, turning mountains of raw information into practical insights that drive real improvements. While factories collect massive amounts of data every day – from production lines to quality control checks – surprisingly, most of this valuable information goes unused. In this article, we’ll explore how manufacturing data analytics is transforming the industry and why it’s becoming essential to stay competitive.
Why Manufacturing Data Analytics Matter
Manufacturing facilities collect an enormous amount of data from their daily operations. For example, production lines, equipment sensors, quality control stations, and inventory tracking systems produce continuous streams of data that could revolutionize manufacturing efficiency. Smart manufacturing data analytics can convert these raw metrics into practical insights that boost productivity and reduce costs. Yet research shows that 70% of this valuable information remains unused.
Companies that implement targeted manufacturing data analysis solutions can spot production bottlenecks before they cause delays. A well-structured manufacturing data lake enables predictive maintenance planning, optimized production scheduling, and enhanced quality control protocols. The right manufacturing data analytics software helps plant managers make evidence-based decisions that lead to measurable improvements.
Manufacturing teams can use these analytical capabilities to reduce downtime, eliminate waste, and maintain consistent product quality standards. The result of smart operations management is that the organization gains real competitive advantages.
Understanding Manufacturing Data Analytics Fundamentals
Manufacturing data analytics unlocks hidden value in production data, helping companies improve their operations through data-driven decision-making. This practical approach combines statistical analysis with continuous monitoring to optimize every stage of the manufacturing process.
Key Components of Manufacturing Analytics
Effective manufacturing analytics relies on multiple integrated systems working in harmony. Machine sensors track performance metrics while specialized quality systems monitor product specifications in real time. These inputs feed into centralized analytics platforms that process both structured data (like temperature readings) and unstructured data (such as maintenance logs) to create clear operational insights.
Real-Time Data Collection and Processing Methods
Modern sensor systems and Industrial Internet of Things (IIoT) equipment provide constant streams of operational data from production lines. A recent McKinsey study found that real-time analytics can cut machine downtime in half. These smart systems monitor critical factors—including temperature fluctuations, pressure changes, equipment vibrations, and power usage—allowing teams to address issues before they become problems.
Impact on Production Efficiency and Quality Control
Manufacturing analytics drives tangible improvements through precise measurement and control systems. Platforms like Hopara help catch quality issues early, saving time and resources. These systems analyze production patterns to determine optimal operating conditions, which leads to less waste and more consistent product quality.
Here are some of the potential benefits:
- Production Improvement: Shorter cycle times through smart scheduling
- Increased Quality: Enhanced consistency through statistical controls
- Cost Reduction: Lower maintenance expenses with predictive care
- Resource Optimization: Better equipment utilization through live monitoring
- Supply Chain Enhancement: Smarter inventory control with accurate forecasting
Essential Features of Manufacturing Data Analysis
Manufacturing data analysis tools continue to advance, providing manufacturers with enhanced capabilities to convert production information into practical insights. These solutions enable companies to enhance quality, minimize waste, and sustain peak production efficiency.
Advanced Visualization Tools for Production Data
Manufacturing visualization tools transform complex production processes into simple, understandable displays. The software converts various inputs—from sensor data to quality measurements—into clear dashboards that reveal important patterns. Manufacturers that implement visualization solutions achieve faster production decisions.
Predictive Maintenance Through Data Insights
Modern analytics systems combine historical equipment data with live monitoring to anticipate maintenance requirements. Machine performance analysis reveals early warning signs of potential breakdowns, allowing teams to address issues before failures occur. This predictive strategy reduces equipment downtime, extends machine lifespans, and enables more efficient maintenance planning.
Quality Assurance and Process Optimization
Manufacturing data analysis supports ongoing quality improvements through precise process monitoring and statistical controls. Analytics platforms continuously examine product specifications, detect variations, and send automatic alerts when measurements exceed set parameters. These functions maintain product quality standards while reducing inspection expenses and material waste.
Manufacturing analytics delivers many essential QA benefits:
- Real-Time Process Control: Quick identification and resolution of quality issues
- Automated Quality Checks: Fewer manual inspection requirements
- Statistical Analysis: Clear visibility into process enhancement options
- Performance Tracking: Ongoing measurement of critical production indicators
- Cost Reduction: Decreased quality-related spending through preventive measures
Real-Time Data Visualization Platform for
IoTLife SciencesData LakesManufacturing
-
Interactive 3D Models
Add relevant context such as floor plans, technical drawings, and maps
-
Semantic Zoom Capability
Effortlessly navigate and drill-down between different levels of detail
-
Configurable Dashboards
Design visualizations exactly how you’d like to see them
Building an Effective Manufacturing Data Lake
Manufacturing data lakes provide essential infrastructure for advanced analytics capabilities by storing massive quantities of production data in native formats. This adaptable structure allows manufacturers to collect and examine information from numerous sources while preserving data quality and ensuring easy access.
Data Lake Architecture for Manufacturing
Manufacturing data lakes need specific architectural planning to manage various types of data. These systems contain structured information from ERP platforms, sensor-generated semi-structured data, and unstructured content such as equipment maintenance documentation.
Integration with Existing Production Systems
The smooth connection between data lakes and manufacturing operations creates a consolidated information environment. This integration enables instant data transmission from production machines, quality monitoring stations, and inventory systems. Success depends on building reliable data transfer channels that preserve information accuracy while delivering quick access for analytical tools.
Data Security and Compliance Requirements
Manufacturing data lakes must satisfy strict security protocols without compromising authorized access. Organizations implement strong authentication measures, encryption standards, and detailed activity monitoring to safeguard sensitive production data. Companies must adhere to ISO 27001 information security guidelines and maintain alignment with local data protection laws.
Implementing Manufacturing Analytics Solutions
Setting up manufacturing analytics demands meticulous planning and robust technology infrastructure to convert production data into tangible results. The right combination of analytical tools and monitoring capabilities forms the essential foundation for optimizing manufacturing processes.
Hopara’s Advanced Manufacturing Data Visualization Platform
Hopara offers a powerful manufacturing data visualization platform that maintains simplicity despite its advanced features. The platform processes raw production metrics that can be used for analytics to highlight areas for enhancement. Production teams gain access to accurate, real-time KPI tracking across multiple lines, making it simple to spot trends and act on opportunities.
Customizable Dashboard Creation
Different manufacturing roles require specific data perspectives to function effectively. The Hopara platform lets users build custom dashboards that show exactly what each team needs to see. While plant managers focus on OEE metrics, quality teams can simultaneously monitor product specs and variable controls. These role-specific views ensure that teams stay focused on their essential metrics while working from the same source data.
Real-Time Performance Monitoring Capabilities
Manufacturing success often hinges on addressing production issues quickly to minimize waste and equipment downtime. According to National Institute of Standards and Technology studies, manufacturers using real-time monitoring see up to 20% better efficiency. Hopara sends immediate notifications when processes stray from target ranges, enabling fast corrections. The system examines equipment performance trends to predict and prevent potential breakdowns.
Schedule a demo to see Hopara’s manufacturing analytics tools in action.
Achieving Manufacturing Excellence Through Data
Smart data analytics has become essential for manufacturers that want to reach peak production performance. Companies that harness advanced visualization tools, predictive maintenance systems, and well-designed data lake infrastructures turn raw operational numbers into concrete actions that enhance productivity and output quality. Hopara’s manufacturing data visualization platform makes this process straightforward with user-friendly dashboards and continuous monitoring features that can suggest clear improvements throughout manufacturing operations.
Manufacturing teams implementing these analytical capabilities see significant reductions in equipment downtime while making smarter decisions about resource usage and consistently meeting rigorous quality benchmarks. This creates lasting advantages over competitors that lack such insights. Manufacturers ready to boost their production efficiency and establish sustainable growth through smart decisions should schedule a demo with Hopara today to see our manufacturing data visualization platform in action.
Real-Time Data Visualization Platform for
IoTLife SciencesData LakesManufacturing
-
Interactive 3D Models
Add relevant context such as floor plans, technical drawings, and maps
-
Semantic Zoom Capability
Effortlessly navigate and drill-down between different levels of detail
-
Configurable Dashboards
Design visualizations exactly how you’d like to see them
FAQs
How does manufacturing data analytics improve material waste reduction?
Real-time tracking through manufacturing data analytics reveals waste patterns and production inefficiencies that often go unnoticed. Smart algorithms examine detailed production records to perfect material usage rates, adjust cutting specifications, and refine manufacturing steps. Plants implementing these solutions have documented material waste reductions of 15-25%, thanks to precise stock control and quality monitoring systems that identify problems during early production stages.
Can manufacturing data analytics predict equipment failures before they happen?
Manufacturing data analytics enables early detection of potential equipment problems through continuous sensor monitoring and advanced machine learning. The technology tracks specific indicators like unusual vibrations, temperature changes, and power usage patterns to spot failing components weeks before actual breakdowns occur. Factories using these analytical tools report 30-50% fewer unexpected stoppages and notice significant improvements in equipment longevity.
What role does manufacturing data analytics play in supply chain optimization?
Manufacturing data analytics creates smarter supply chains through accurate sales predictions, balanced inventory management, and improved supplier relationships. The technology examines past sales data, current market indicators, and factory schedules to maintain perfect stock levels while reducing storage expenses. Most manufacturers see inventory cost savings of 20-30% after implementation, without sacrificing customer service quality.
How can manufacturing data analytics improve energy efficiency in production facilities?
Smart sensors connected to manufacturing data analytics systems track power usage across machines and production lines, pinpointing energy waste sources. The software studies peak consumption times, equipment performance metrics, and production timing to create effective power-saving plans. Most facilities achieve 15-25% lower energy bills after following these data-driven recommendations.
What security measures protect sensitive information in manufacturing data analytics systems?
Manufacturing data analytics platforms use strong security features such as complete data encryption, strict user permissions, and active threat monitoring. Regular system checks, automatic data backups, and security compliance testing guarantee information safety. These platforms create detailed activity records and use advanced login methods, keeping data protected while authorized staff maintain quick access to their needed information.
Want to learn more how Hopara can help you?
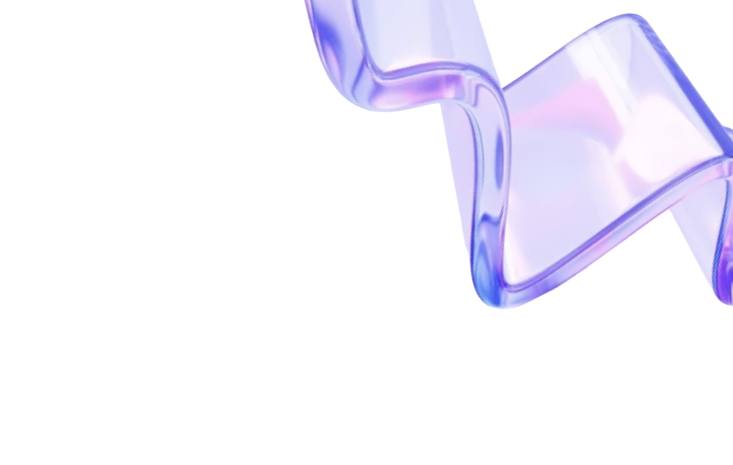
