- Blog
Reduce Downtime in Manufacturing with Real-Time Analytics
Manufacturing downtime can strip away as much as $260,000 per hour from a company’s bottom line, according to Aberdeen Research findings. When production stops, businesses face immediate revenue losses, missed delivery targets, and upset customers.
Real-time data analytics offers a practical solution to prevent these costly shutdowns. Smart monitoring systems can detect early warning signs of equipment problems, helping manufacturers reduce downtime in manufacturing by up to 50%. These systems continuously track machine performance and send immediate notifications when issues arise.
Many facilities have successfully implemented manufacturing downtime prevention strategies through targeted sensor placement and automated alert systems. The key to reducing downtime in manufacturing lies in collecting and analyzing equipment data consistently. Manufacturing teams can spot potential failures days or weeks before they occur, schedule maintenance during off-peak hours, and keep production running smoothly. This approach helps facilities maintain optimal efficiency while avoiding unexpected interruptions.
Understanding Manufacturing Downtime
Manufacturing downtime occurs when production equipment stops operating, creating a direct hit to productivity and revenue. Learning to manage these interruptions effectively helps manufacturing teams maintain consistent output and meet production targets.
What Constitutes Manufacturing Downtime
Two main categories define manufacturing downtime: planned and unplanned stops. Planned downtime includes essential activities like routine maintenance, equipment updates, and regular shift transitions. Unplanned downtime, which creates the most costly disruptions, stems from unexpected equipment failures, sudden power losses, or supply chain interruptions. Manufacturing facilities typically lose 5-20% of their production capacity due to unexpected equipment failures and related issues.
Impact on Production Efficiency
Equipment failures create a chain reaction throughout the production process. Staff members wait idly, materials have the potential to become unusable, and delivery schedules get pushed back. These delays often strain relationships with customers and affect the company’s reliability rating. Manufacturing plants that implement proper monitoring systems experience significantly fewer production interruptions than those operating without such equipment tracking tools.
Key Performance Indicators for Downtime
Measuring specific metrics helps manufacturing teams identify and fix downtime issues quickly. Three key performance indicators provide the clearest insight into equipment reliability and efficiency:
- Overall Equipment Effectiveness (OEE): This metric combines availability, performance, and quality to show how efficiently a manufacturing asset is operating. A high OEE score means equipment is running at peak productivity with minimal losses.
- Mean Time Between Failures (MTBF): MTBF tracks the average time equipment operates before experiencing a failure. Higher MTBF values indicate more reliable machines and fewer unexpected breakdowns.
- Mean Time to Repair (MTTR): MTTR measures how long it takes to repair equipment after a failure occurs. A lower MTTR means issues are resolved faster, minimizing production disruptions.
These indicators show exactly how well equipment performs and where maintenance efforts need focus. Real-time monitoring systems can track these measurements automatically, giving manufacturing teams instant insights into machine performance and helping them spot potential problems early.
Identifying Common Causes of Production Stops
Manufacturing interruptions create significant challenges for production teams. Finding the specific reasons behind these stops can help organizations implement targeted fixes and maintain steady output levels.
Equipment Failures and Maintenance Issues
Equipment breakdowns represent a major portion of unexpected manufacturing downtime. These stoppages typically stem from mechanical component wear, electrical system problems, and missed maintenance checks. Manufacturing facilities can catch potential issues through consistent equipment checks and automated monitoring systems that detect unusual equipment behavior like excessive vibration, abnormal temperatures, or reduced performance metrics.
Process Bottlenecks and Inefficiencies
Manufacturing lines often experience slowdowns from process bottlenecks that affect the entire production chain. Common trouble spots include material transport systems, quality inspection points, and assembly areas. Production teams use advanced monitoring tools to spot these constraints through detailed analysis of output rates and equipment usage data. Continuous tracking shows exactly when materials start backing up or processes become delayed, letting teams make quick operational adjustments.
Human Factors and Training Gaps
Employee-related factors make up a significant portion of manufacturing downtime. Production stops frequently occur due to operational mistakes, insufficient training programs, or unclear work procedures. Advanced production systems help reduce these issues through detailed digital instructions for each task. These platforms measure worker performance and identify specific areas where extra training could improve overall efficiency. Manufacturing facilities that focus on worker education and digital support tools see meaningful reductions in operation-related stoppages.
The table below summarizes typical downtime events and their impacts and means of prevention.
Downtime Cause | Average Impact | Prevention Method |
---|---|---|
Equipment Failure | 42% of unplanned stops | Predictive maintenance, sensor monitoring |
Process Bottlenecks | 28% of efficiency loss | Real-time analytics, flow optimization |
Human Factors | 30% of production errors | Digital work instructions, targeted training |
Real-Time Data Visualization Platform for
IoTLife SciencesData LakesManufacturing
-
Interactive 3D Models
Add relevant context such as floor plans, technical drawings, and maps
-
Semantic Zoom Capability
Effortlessly navigate and drill-down between different levels of detail
-
Configurable Dashboards
Design visualizations exactly how you’d like to see them
Measuring the True Cost of Downtime
A thorough understanding of downtime expenses reveals significant financial impacts, from immediate costs to lasting operational effects.
Direct Financial Losses
When production lines stop, companies face substantial monetary losses through missed targets and labor expenses. Research indicates that manufacturing facilities lose $30,000-50,000 hourly during equipment failures. These expenses include material waste, overtime costs for production catch-up, and expedited shipping charges to maintain delivery schedules. Smaller manufacturing operations often experience greater relative impacts since they rarely have backup equipment to maintain partial production during breakdowns.
Hidden Costs and Long-Term Effects
Manufacturing downtime creates numerous indirect expenses that significantly impact bottom lines. Late deliveries decrease customer satisfaction and often result in canceled future orders. Production stops frustrate workers, leading to increased turnover rates. Equipment pushed beyond normal operating speeds to recover lost time experiences faster deterioration, requiring more frequent replacements and maintenance.
Calculating Return on Investment for Solutions
Manufacturing teams must examine both implementation expenses and potential savings when selecting downtime prevention tools. A standard monitoring system investment of $50,000 per year that prevents two monthly hours of downtime typically recovers its cost within three months. Successful manufacturing operations monitor these essential metrics:
- Production value losses per hour
- Workforce costs during stoppages
- Repair and maintenance expenses
- Customer satisfaction scores
- Equipment longevity metrics
- Power usage measurements
Real-time monitoring systems like Hopara enable manufacturing teams to track these measurements automatically. The platform warns operators about potential problems before they cause production stops, enabling scheduled maintenance during planned downtimes. This prevention-focused strategy typically cuts unexpected manufacturing downtime by 30-45%, resulting in significant cost reductions. Try Hopara to discover how data analysis can protect your production from expensive interruptions.
Real-Time Data Solutions for Downtime Prevention
Manufacturing facilities reduce equipment failures through data-focused methods that identify issues before they cause complete shutdowns. Smart monitoring tools and detailed analysis systems work hand in hand to keep production lines running smoothly.
Advanced Analytics and Predictive Maintenance
Manufacturing professionals rely on specialized computer algorithms to detect potential equipment problems early. These tools continuously examine equipment data like temperature changes, unusual vibrations, and performance indicators to schedule timely maintenance. Research indicates that companies using these preventive approaches see significant reductions in equipment failures and longer machine lifespans.
Implementing Smart Monitoring Systems
Strategic sensor placement forms the foundation of effective downtime prevention. Modern equipment sensors constantly track essential measurements, including energy use, heat levels, and machine speed. The system sends immediate alerts to maintenance teams when measurements indicate potential problems. This quick notification system helps factory staff fix small issues before they escalate into production-stopping breakdowns.
Using Hopara for Real-Time Production Insights
Hopara’s visualization tools turn raw manufacturing data into easy-to-understand performance metrics. The platform connects to equipment sensors directly and shows live statistics on custom-built displays. Factory teams can set specific warning levels for individual machines and get quick notifications about developing problems. This focused monitoring helps maintenance crews organize their work better and plan repairs during scheduled maintenance windows. Try Hopara to learn how live equipment monitoring can help maintain your production efficiency.
Strategic Steps for Long-Term Success
Manufacturing downtime presents significant challenges for production facilities, making systematic prevention essential for operational success. Companies that implement continuous data monitoring alongside detailed performance analysis gain a clear advantage in spotting potential issues. Equipment tracking systems help maintenance teams identify small problems before they escalate into major failures, keeping production lines moving smoothly while minimizing unexpected stops.
Hopara can help you unlock advanced equipment monitoring capabilities and start preventing costly production interruptions before they impact your bottom line.
Real-Time Data Visualization Platform for
IoTLife SciencesData LakesManufacturing
-
Interactive 3D Models
Add relevant context such as floor plans, technical drawings, and maps
-
Semantic Zoom Capability
Effortlessly navigate and drill-down between different levels of detail
-
Configurable Dashboards
Design visualizations exactly how you’d like to see them
FAQs
How does downtime in manufacturing affect worker morale and retention?
Manufacturing employees experience significant stress when production lines stop frequently, which directly impacts attendance rates and staff turnover. Workers often face unexpected schedule adjustments and extra shifts due to these interruptions, making them more likely to seek employment elsewhere. This constant disruption typically leads to reduced workplace satisfaction and makes it challenging to keep experienced team members.
What role does inventory management play in reducing downtime in manufacturing?
Strong inventory management systems minimize manufacturing downtime through careful tracking of essential components and materials. Advanced stock control methods predict usage patterns and trigger automatic reorders, ensuring that replacement parts remain available. This approach prevents production stops caused by missing components or depleted supplies.
How can manufacturers measure the effectiveness of their downtime prevention strategies?
Companies need to monitor key indicators such as equipment failure rates, maintenance response times, and the financial benefits of prevented shutdowns. Advanced monitoring equipment provides detailed analytics showing exactly when and where manufacturing downtime was prevented, helping teams refine their prevention methods.
What impact does seasonal variation have on manufacturing downtime?
Weather changes create additional manufacturing downtime risks through temperature swings and moisture level changes that stress equipment. Plants typically see increased equipment failures during harsh weather periods, making seasonal maintenance adjustments essential for reliable operations.
How does poor communication contribute to downtime in manufacturing?
Gaps in communication between teams often make manufacturing downtime worse as critical information about equipment issues gets delayed or lost. Setting up specific procedures for sharing maintenance updates and equipment status helps teams respond faster to problems and reduces unnecessary production interruptions.
Want to learn more how Hopara can help you?
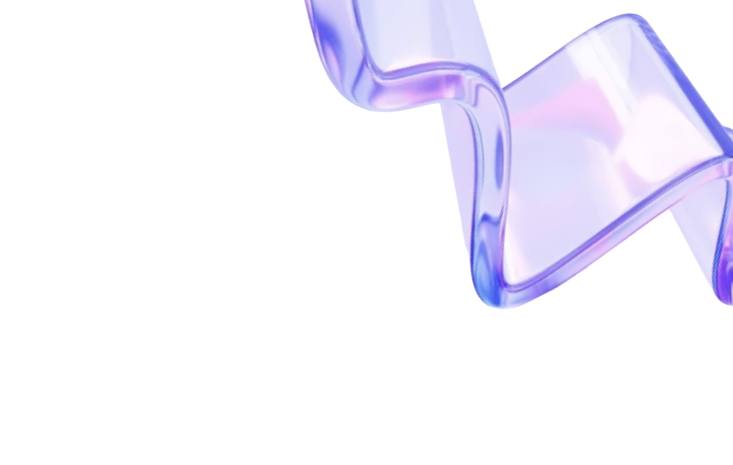
